This guide to wood floor finishing and renovation helps you make the choices that are an integral part of the finishing process to achieve the appearance on a wood floor that will best fit your décor and lifestyle. The type of finish, the stain choice, and the sheen are the basic choices to be determined. A basic knowledge of the finishing process provides a better understanding of the work process and timeline. However, a Southern Wood Floors specialist can assist you with more specific knowledge of items like finish brands and curing times related to each floor product and design as well as advanced finish techniques to achieve the look you want in your wood floor.
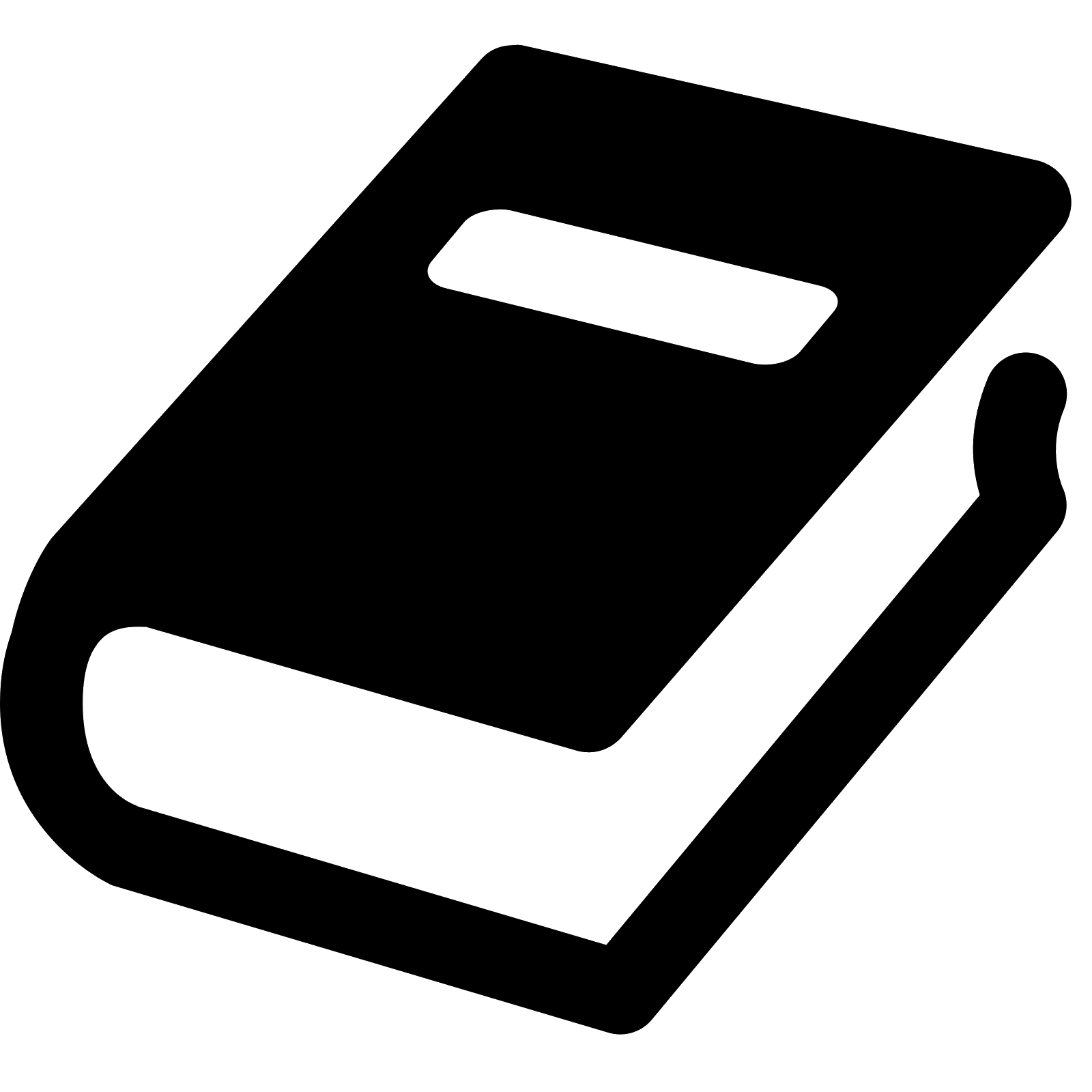
Woof Floor Finishing Summary
This summary is compiled based on industry standards set forth by the National Wood Flooring Association and infield experience. It is not intended to cover all aspects in detail but allow the client an overview of the most important finishing elements that are part of any successful wood floor. Southern Wood Floors wood floor specialists can provide specific details of finishing methods and specific floor finishing products. Our goal in this summary is to outline the process in order to better provide an overview of the time line required in the finishing process as well as assist in understanding the choices required.
Jobsite Conditions:
- If wall coverings and painting are completed prior to finishing, it is imperative that these elements are dry. Conversely, if these elements are to be completed after finishing of floor, it is important to be sure that final floor finish coat is dry and cured.
- In the refinishing of existing floor, the shoe mold or quarter round must be removed.
- Evaluate the floor for board repair prior to sanding.
- It is important to evaluate and determine any light fixtures, sensitive equipment or appliances, or valuable properties that should be protected in the finishing process. A discussion of the appropriate way to cover and protect should be discussed. Even the best low dust systems are not dustless. Appropriate plastic should be used to seal work areas and specific items that are identified with the finishing professional.
- 220 power is required to operate some sanding equipment. If your project is new construction, access to 220 power will be required in a safe manner.
General Sanding Process:
- The times a wood floor can be sanded depends on the skill of the wood floor professional, the equipment used, the existing wear layer and the overall flatness of the floor. It is always important to evaluate the remaining wear layer on existing floors to determine if a floor can be sanded.
- Sanding is a process completed with various grits of paper in progression. The first grit is determined by judging the flatness of the floor and the depth of any damage. This first cut allows the flatness to be restored and damage to be removed. Depending on the depth of damage it may not be practical to remove all damage.
- The successive grits allow the first grit lines to be removed and begin the smoothing process that is completed with sanding screens.
- Every floor is different and the sanding progression is evaluated for each floor. Our floor finish technicians are glad to discuss the incremental sand grits and steps needed to prepare for floor for the finishing process.
General Finishing Process:
-
- Once the sanding is complete, choice of color becomes the next critical decision. From the onset of floor choice, every effort to provide the information necessary to achieve an appearance should be considered. At this stage, the floor chosen should lend its self to the final appearance. For example, if the final appearance is to emphasize brown and other earth tones, a white oak base allows the stain needed to enhance the natural colors of the floor. If red oak where the base, then the stain chosen must compensate for trying to remove the underlying pinks and reds.
- Our floor technician will work with you onsite to achieve color depth and intensity. This is best done by testing stains on the actual floor versus making a final decision from a single sample board.
- Allowing the stain to dry thoroughly is a key factor for the first finish coat to adhere. This varies by stain, stain amount applied, humidity, wood species, air circulation and temperature. Given these variables, every attempt is made to keep timelines updated based on this choice point in the finishing process.
The finish choice is next. Choices of finish types are summarized below; however specific brands we support can be found in the “Finish Products” tab for brand specific information. Please note that information is not provided in this overview regarding wear expectations or hardness. Each brand makes claims regarding those points but we often find client appearance and wear expectations are more important than scientific abrasion test results. Each finish has pros and cons that directly relate to the use and wear intended. Southern Wood Floors always makes an effort to assist the client in understanding finish expectations. All finishes will scratch and wear. All floors regardless of specie will indent.
Oil Modified Finish – This is the traditional and currently the most widely used. The urethane is suspended in oil base distillates that dries by solvent evaporation and cures with the reaction of polyurethane with other driers and oxygen. Sheens available are normally satin, semi-gloss, and gloss. Some designer sheen options are available such as “dull rubbed” or matte. Based on most system recommendations, this is a 2-3 coat process requiring drying times and abrasion between each coat. Most coats dry in 24 hours between coats but longer drying periods may be required.
Water Based Finish – This finish suspends the urethane in water and dries and cures by water evaporation. Sheens available are normally satin, semi-gloss, and gloss. Based on most system recommendations, this is a 2-3 coat process. The drying time between coats is normally 4-8 hours or sooner depending on conditions. This allows successive coating to reduce overall finishing times.
Water Oil Modified Finish – This finish combines both oil based urethanes and water suspension to allow for quick dry. Generally available in a satin and gloss sheen. This is system is normally a 2-3 coat process. The drying time between coats is normally 4-8 hours or sooner depending on conditions. This allows successive coating to reduce overall finishing times.
Modified Tung Oil Finishes – This finish includes a suspension of Tung oil in solvents and dries that provides a “yesteryear” appearance. Providing a look on pines and reclaimed wood projects, this finish is normally applied in a 3 coat system. Drying times between coats are normally 24 hours depending on environmental conditions. Sheens are gloss and satin.
Hard Oil Finish – This finish is a combination of plant based oils that normally applies in a single coat to bond with the wood fibers. Available in a wide range of colors as well as natural the sheen is considered matte or satin only. This finish is normally applied in a single coat application with some systems requiring an additional top coat.
Wax – This traditional finish is seldom used in the current market based on the continued up keep required. The system is normally applied in 1-3 coats and requires periodic buffing to maintain a wax luster.
Moisture-Cured Urethane – This finish although still available is rarely used due to strong odor, flammability, and respiratory requirements. Having an old reputation of being the hardest finish, many of these assumptions have been dispelled.
Finally, understanding the finishing process and finish products can assist in getting the appearance desired in a wood floor and the time frame expectations for completion. Choosing the right finish will help meet expectations of appearance and wear. Southern Wood Floors can work with each project to guide finish and appearance choices by understanding each project. Most importantly, gaining the knowledge of how the finish will dry and ultimately cure can ensure that re entry to the project allows for the best possible wear.
Please find below a brief glossary on finish terms that may assist in understanding the finish process lingo that may be used in conversation.
Sanding and Finishing Glossary
Abrasives – These are the sanding belts, screens, edger discs, and pads that have various grits from fine to coarse used on large sanding machines, buffers, and edgers.
Adhesion – Simply, the reason one material sticks to another. This is important in applying multiple finish coats. Factors such as being chemically clean and not too smooth, hard or nonporous determine adhesion.
Amber – A yellowish golden color that can change from the wood or finish. Some finishes will have amber tints others will be neutral.
Bond – The adhesion between two un-similar materials.
Cure – In reference to finish, this is the state that a chemical action or reaction has occurred versus drying.
Cut – a reference to the sanding of a floor with the sanding equipment. Usually in reference the progression on grits.
Distressed – A texturing of the floor by scrapping, scratched, denting, gouging or other methods to achieve a worn or antique appearance.
Dry to Tack/Touch – a reference to a finish coat not being stick or tacky to the finger
Dry to Sand– The stage of dry that allows for re coat without softening, sticking or clogging the sand paper or screen.
Dry to Dust – The stage of dry that small dust particles will not stick to finish.
Filler – used to fill holes or defects in floor surface. Some filler may be used prior to sanding and others are used after finishing is complete.
High Solids – referenced in finishes to distinguish the percentage of solid ingredients to solvent. Normally a high solid is preferable for final and build finish coats.
Sealer – Initial coats of finish that stop the absorption of succeeding coats. Shade – the degree of color in the stain.
Sheen – The luster of the dry finish. Normally referenced as gloss, semi-gloss, satin. Other references may be used for unique sheens like dull rub or matte.
Staining – Use a pigment, chemical or dye to change the color of wood without changing the texture or grains.